stainless steel high temperature creep|316 stainless steel creep strain : private label Once the design parameters have been established, the engineer may then evaluate the materials that appear to be capable of meeting the design strength requirements. For . See more web26 de dez. de 2023 · No aguardo pela versão oficial do Brasfoot 2024, O Brasfoot 2024 Superpatch eleva sua experiência de Manager a novos patamares, oferecendo uma .
{plog:ftitle_list}
Ganhe R$100 de graça, saques rápidos Pix.verificado como real e eficaz
There are four design factors that engineers consider when choosing materials for service at elevated temperature. These design factors are: Service life Allowable . See more
Once the design parameters have been established, the engineer may then evaluate the materials that appear to be capable of meeting the design strength requirements. For . See moreAnother factor to consider in designing for high-temperature service is the amount of deformation that can be permitted during the total service life. . See moreThe effect of exposure of a material to media can be a very complex subject. Elevated temperatures tend to increase corrosive action, heat transfer may affect corrosivity, thermal cycling can increase metal wastage through spalling of protective scale on . See more Although 316 steel grades have been studied for the service conditions of current nuclear and other conventional applications, improved data and models for the long term high .
316LN stainless steel constitutes one of the principal research and development areas for SFR core materials (Jayakumar et al., 2013). 316LN compensates for the loss resulting from decreasing carbon content during solid solution strengthening by increasing its nitrogen content. . The high-temperature creep test conditions (temperature is . Creep and creep damage behavior of stainless steel 316L manufactured by laser powder bed fusion. Author links open overlay panel L.A. Ávila Calderón a, B. Rehmer a, S. Schriever a, . MTS water-cooled high-temperature single-side extensometers (Model: 632.51C-03, class 1, nominal gauge lengths 50 mm and 52 mm) are used to measure the strain. . The creep behavior of Fe–17Cr–1.2Cu–0.5Nb–0.01C ferritic heat-resistant stainless steel was investigated at temperatures ranging from 973 to 1123 K and stresses from 15 to 90 MPa. The evolution of precipitates after creep deformation was analyzed by scanning electron microscopy, energy dispersion spectrum, and transmission electron microscopy. The .
high temperature metal creep testing
Creep Buckling of 304 Stainless-Steel Tubes Subjected to External Pressure for Nuclear Power Plant Applications. . Norton, F.H. Creep of Steel at High Temperatures; McGraw-Hill: New York, NY, USA, 1929. [Google Scholar] Weertman, J. Theory of steady-state creep based on dislocation climb. J. Appl. Creep behavior of AISI 316 austenitic stainless steel as one of the most fundamental materials utilized in high temperature operating conditions due to their good high-temperature mechanical . Ferritic stainless steels have lower high-temperature strength than corresponding austenitic stainless steels with similar chromium contents, which is one of the key determinants for durable operation in creep and thermal fatigue tests [].Improving the high-temperature strength of ferritic stainless steels has become an important research topic. High-temperature creep rupture life of 304L stainless steel for different laser powers. 3.2. Relative density. . In the present study, high-quality 304L stainless steel samples have been manufactured by the selective laser melting technique. The effects of laser power on the permanent life, relative density, porosity, and hardness of the as .
The creep deformation behavior and creep mechanisms of nanocrystalline 316L austenitic stainless steels at high temperature with different peak stresses are investigated by molecular dynamics simulations. Numerical results demonstrate that the creep deformation of nanocrystalline 316L austenitic stainless steels at high temperature is caused by the .
High-temperature processes induce creep and corrosion, primarily resulting in failure of thin-walled pressure vessels. Investigating alloy creep behavior in these vessels is crucial due to its often undetected nature, leading to sudden and costly failures, posing irreversible risks to health and the environment. This study investigates the creep behavior of . The creep deformation behavior and age strengthening behavior of 304 stainless steel under high stress levels were systematically studied by uniaxial creep test, tensile test, XRD diffraction test and transmission electron microscopy. The results show that the total creep strain and the initial creep strain rate increase with the increase in stress level, and the creep .Interpretation of High-Temperature Creep of Type 304 Stainless Steel O. K. CHOPRAAND K. NATESAN The elevated-temperature creep behavior of Type 304 stainless steelis examined in terms of the measured effective and internal stresses. Results show that the mean ef-fective stressis relatedtothe appliedstressby a power law of the form a* = ~(a)~, Stainless steels subjected to constant load at high temperature, such as under creep conditions, are known to develop microstructural changes including precipitation of distinct phases.
In the following sections, we first describe the austenitic stainless-steel material (AISI 304) examined in this study, the methods used to probe its high-temperature viscoelastic relaxation, and the strategies employed in processing the data and fitting the (G, Q −1) data to a Burgers creep-function model.The data, spanning a wide range of temperature and . Creep life, high-temperature tensile properties of creep strength enhanced ferritic-martensitic P92 steel and austenitic 304L stainless steel (SS) dissimilar weld joint were investigated. DWJ was prepared using tungsten inert gas welding process employing ERNiFeCr-2 (Inconel 718) filler metal. The creep tests were conducted at 650 °C under stresses ranging 80 .The elevated-temperature creep behavior of Type 304 stainless steel is examined in terms of the measured effective and internal stresses. Results show that the mean effective stress is related to the applied stress by a power law of the form sigma* = ..cap alpha..(sigma)/sup ..beta../, where the constants ..cap alpha.. and ..beta.. are functions of temperature.
Creep strength can thus be improved by increasing the grain size, a method commonly employed in the design of austenitic stainless steel and carbon steel. Modeling and Testing Creep Behavior Testing the creep . literature surveys on specific aspects of creep and high-temperature deformation so that the readers . The creep-buckling behaviors of cylindrical stainless-steel tubes subjected to radial . This expansion coefficient not only varies between steel grades, it also increases slightly with temperature. Grade 304 has a coefficient of 17.2 x 10-6 /°C over the temperature range 0 to 100°C but increases above this temperature. The effect of thermal expansion is most noticeable where components are restrained, as the expansion results in buckling and bending.
In order to achieve the high-temperature creep test with a small amount of sodium (23.00 ± 0.5 g), bellows and sodium storage tube made of 347 stainless steel are utilized. The sodium environment of the specimen is achieved through .understanding of the mechanisms of creep. Creep and High Temperature Failure Dr. M. Medraj Mech. Eng. Dept. – Concordia University MSE 521 Lecture 14/3 Creep and High Temperature Failure • Constant load applied at constant “ high” temperature • Deformation as a function of time ( vs. t) • Three stages of creep: Iega •St (primary . Therefore, information on the high temperature creep behavior is needed for a better understanding of the mechanical behavior of the new alloys, their practical applications, and the comparison with conventional alloys. . Data sheets on the elevated-temperature properties OF 18Cr-10Ni-Nb stainless steel tube for boilers and heat exchangers .
The temperature ranges specified (600–850°C for creep and 25–700°C for fatigue) cover conditions relevant to high-temperature applications where stainless-steel components may be subjected to either cyclic loading or sustained loading over time. This study reports the significant ambient temperature creep plasticity at stresses below the conventional 0.2% plastic strain off-set yield stress. This is partially due to the relatively high strain-rate sensitivity of 304 stainless steel. Cold-working significantly increases the creep resistance. Descriptive equations that predict low-stress creep plasticity, which are somewhat .Theestablished creep analytical modeling was used to predict the creep life of stainless steel at high temperature. In order to conduct creep testing, the materials were subjected to constant load and high temperature at 565oCin comparisons with different stresses at the similar temperatures.Time dependent deformation of 316L stainless steel at .
A family of creep-resistant, alumina-forming austenitic (AFA) stainless steel alloys is under development for structural use in fossil energy conversion and combustion system applications. The AFA alloys developed to date exhibit comparable creep-rupture lives to state-of-the-art advanced austenitic alloys, and superior oxidation resistance in the ~923 K to 1173 K .
The creep rupture specimens were machined from Super304H steel tube as shown in figure 1. Creep tests were carried out at 600, 650, and 700 C from 1 to 13,000 h. It was shown that the predicted creep–fatigue lives were in good agreement with the experimental data for AISI 304 stainless steel and AISI 316 stainless steel for various hold time periods [4]. However, the available data used to check the reliability of the model was very limited, since they covered with only one or two strain ranges.
high temperature metal creep examples
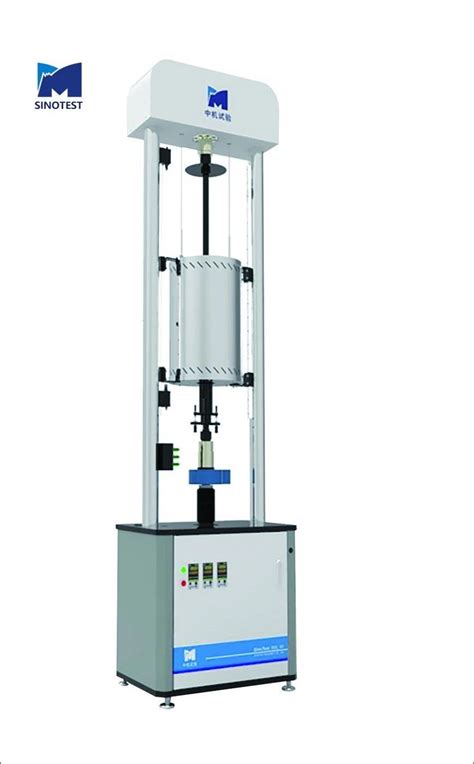
high temperature materials creep
plant moisture meter jumps around
WEBCubatão - 19996920167 - R$150. Anúncio: Este site está a venda, aceitamos propostas, [email protected] ! Listamos as melhores acompanhantes em Itapira (SP) no .
stainless steel high temperature creep|316 stainless steel creep strain